Metal detection is essential for the food processing and packaging industry. Not only do metal detectors protect the processing equipment, but they are also important in ensuring product purity and consumer safety. But have you ever wondered how metal is detected and removed during food processing? Metal detection is a two-step process. When metal has been detected, it and the contaminated product must be removed from the process.
Removing Metal Contaminants in Packaged Food Processing.
Following are common methods of removing metal contaminants from conveyed “packaged” food product.
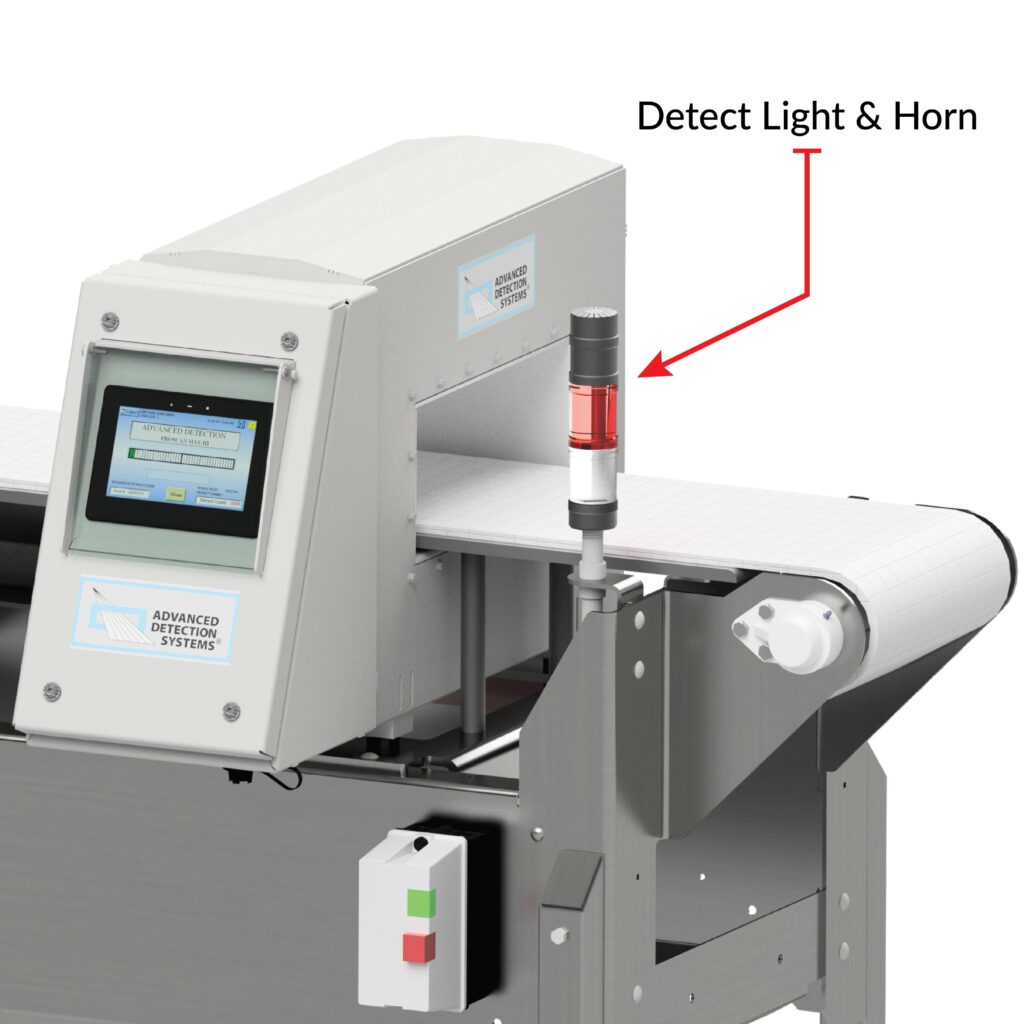
Stop on Detect.
When metal is detected, electronic outputs from the metal detector are used to stop the conveyor motor and actuate a detect light and/or horn mounted on the metal detector conveyor. This method is typically used for packaged food product. When the conveyor stops a worker is held responsible for removing the packages from the conveyor downstream of the metal detector. The packages are run through the detector again to isolate those that are contaminated with metal. The contents of the contaminated package(s) are divided and passed through the detector until all of the metal contaminant that tripped the detector is found. In all cases described here this procedure is to be followed by an investigation into the source of the metal leading to changes in the production process that will prevent another similar occurrence.
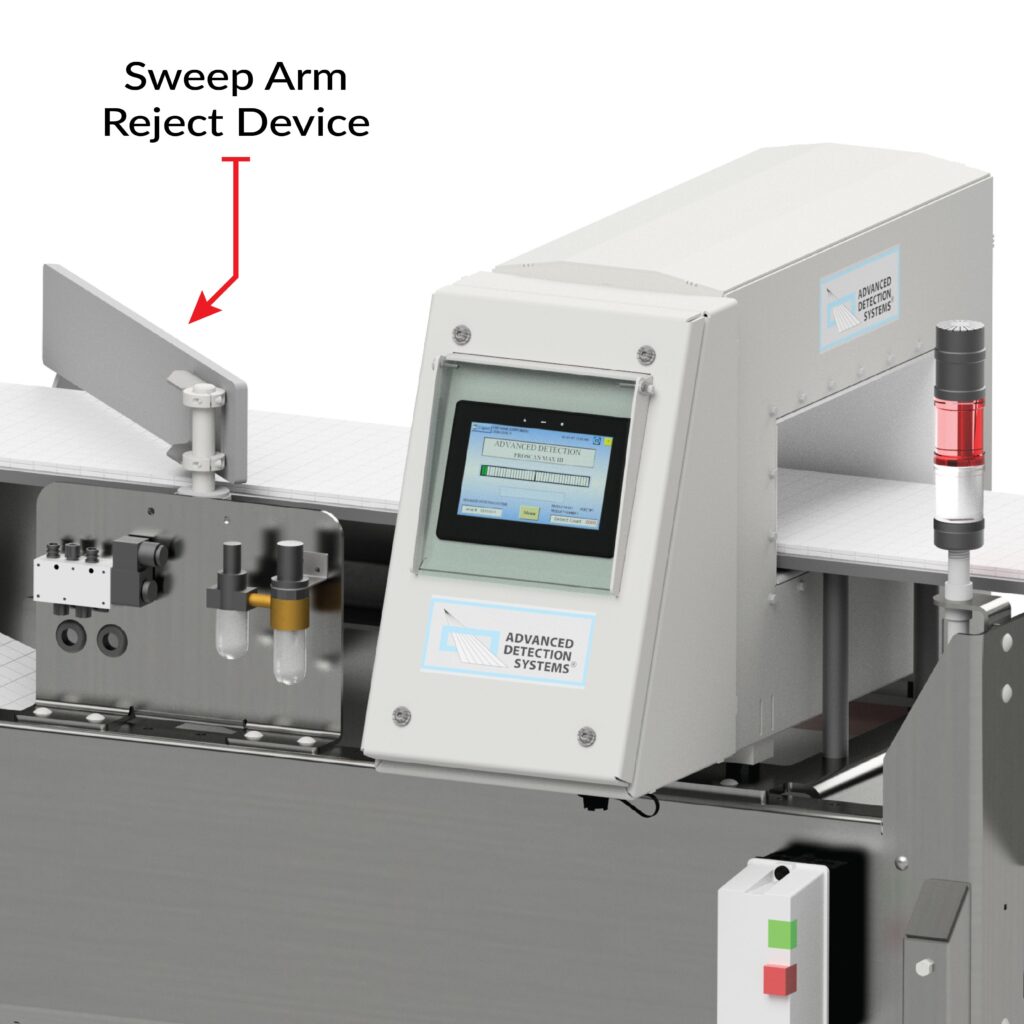
Automatic Sweep Arm or Ram Reject.
When metal is detected an electronic output from the metal detector actuates the reject device which is timed to move packaged, boxed or bagged product off the side of the conveyor and onto a tray or into collection bin.
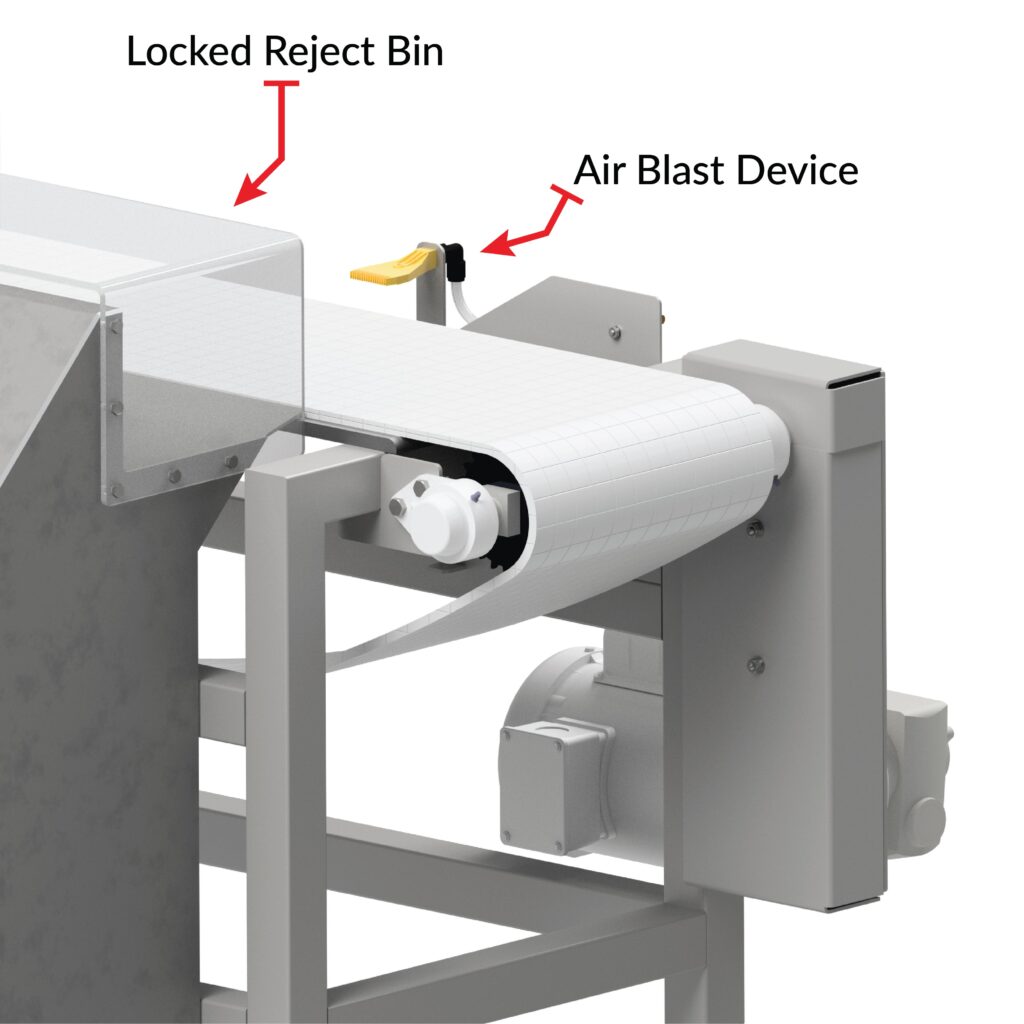
Automatic Air Blast Reject.
When metal is detected an electronic output from the metal detector releases a strong blast of air that is timed to push packaged product off the side of the conveyor into a collection bin. The air blast reject is used in food processing when the conveyor belt is 12” wide or less and packaged product typically weighs 5 lbs. or less with a flat surface to catch the blast of air.
Removing Metal Contaminants in Bulk Food Processing
Following are common methods of removing metal contaminants from conveyed “bulk” food product. As with packaged product, bulk product is divided and run through the food processing metal detector again and again until the contaminated product and the contaminant itself is located.

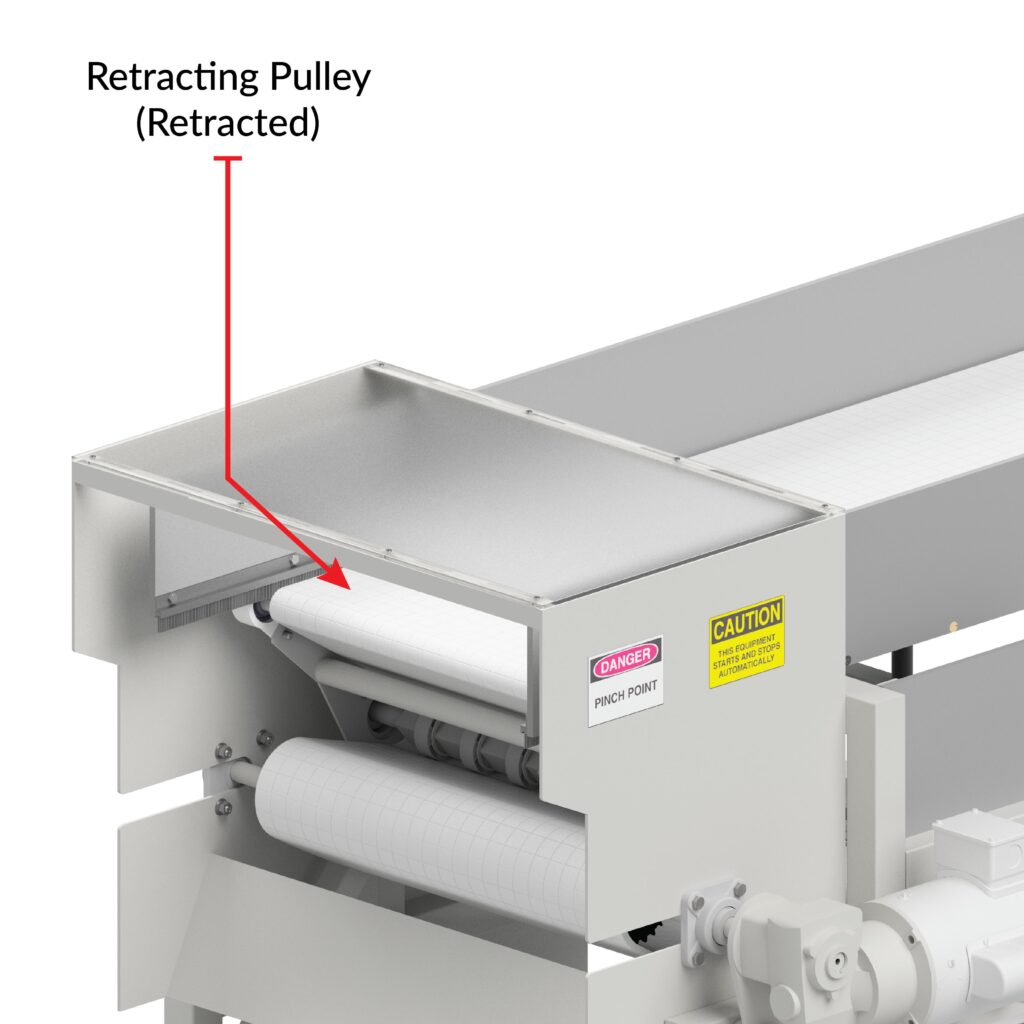
Retracting Pulley Reject.
When metal is detected a timed electronic output from the metal detector retracts the pulley on the discharge end of the metal detector conveyor creating a gap between the conveyor discharge and the in feed of the conveyor product is being transferred to downstream of the metal detection system. This allows the contaminated food product to drop through the gap into a collection bin.
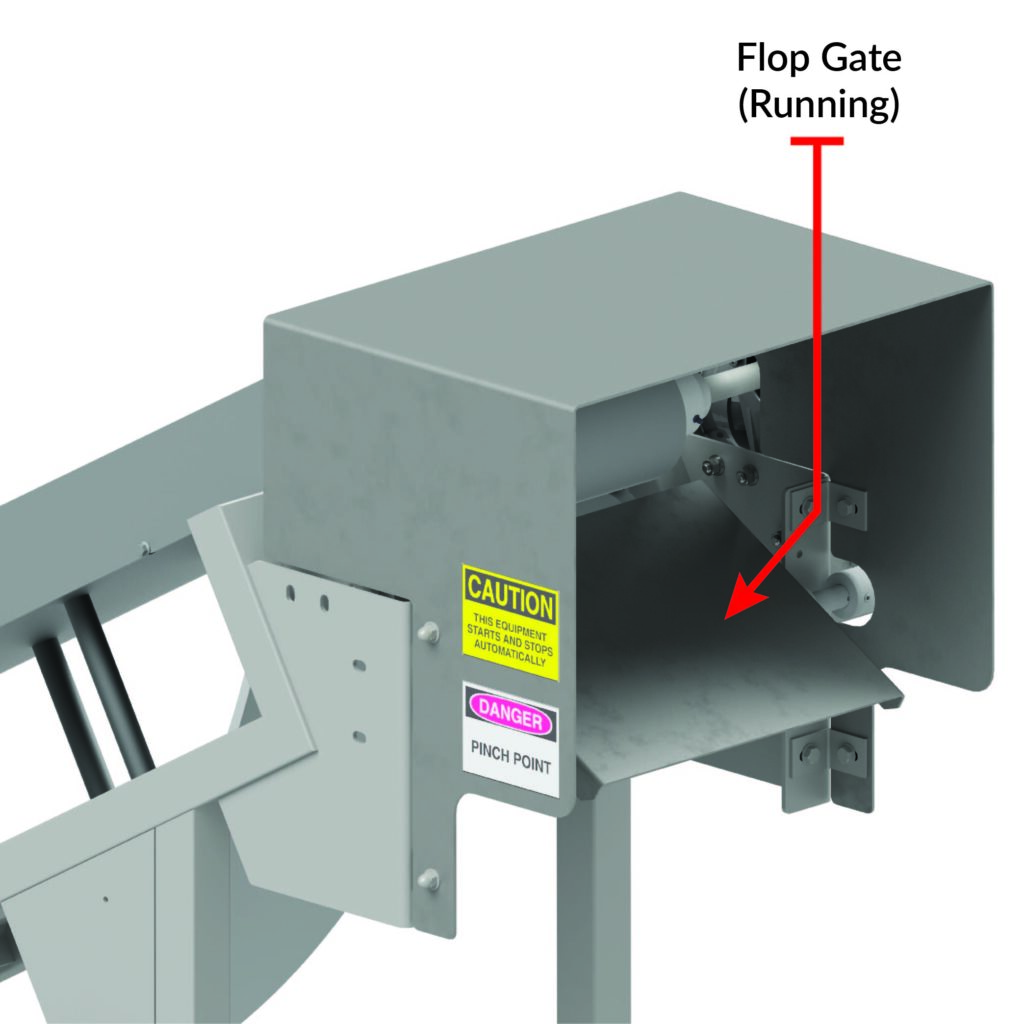
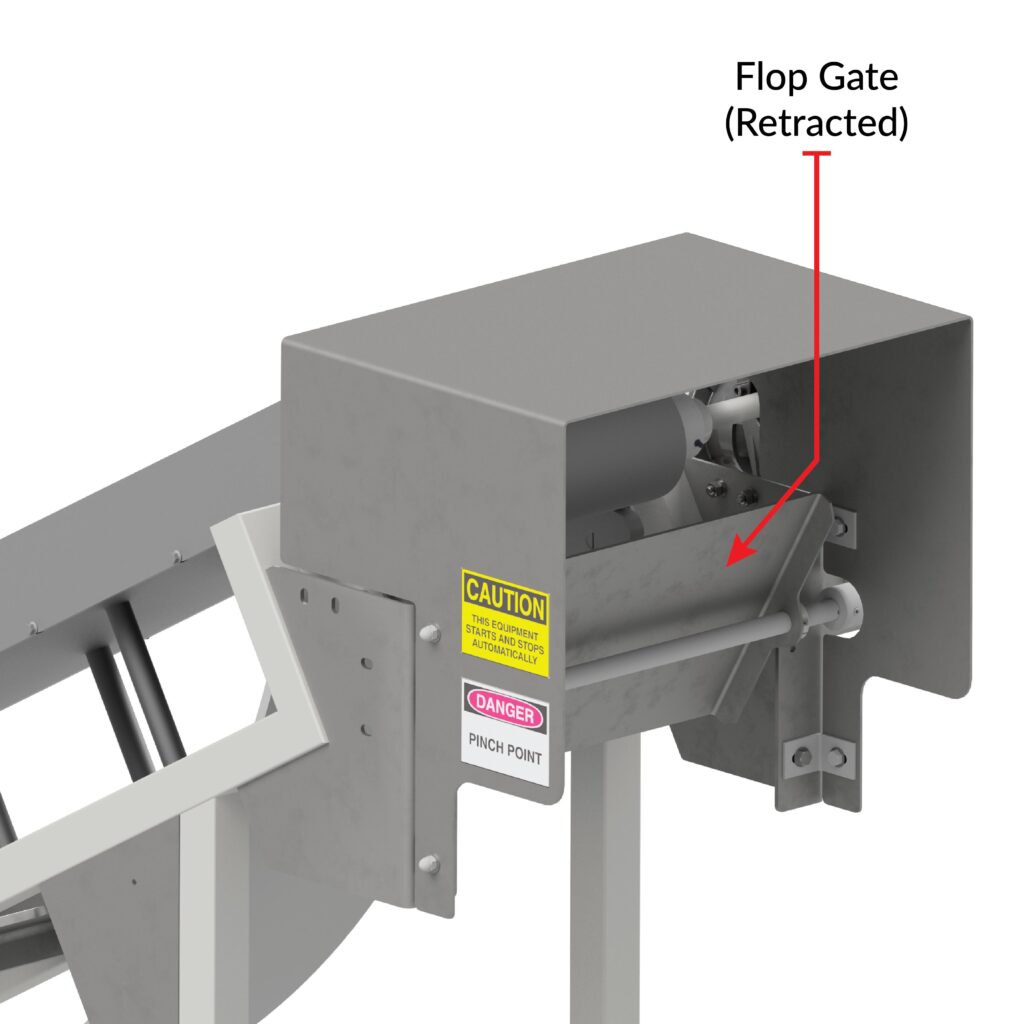
Flop Gate Reject.
When metal is detected a timed electronic output from the food processing metal detector flips the gate at the discharge end of the metal detector conveyor redirecting product into a bin underneath the discharge end of the conveyor.
Other Food Processing Metal Detection & Rejection Systems
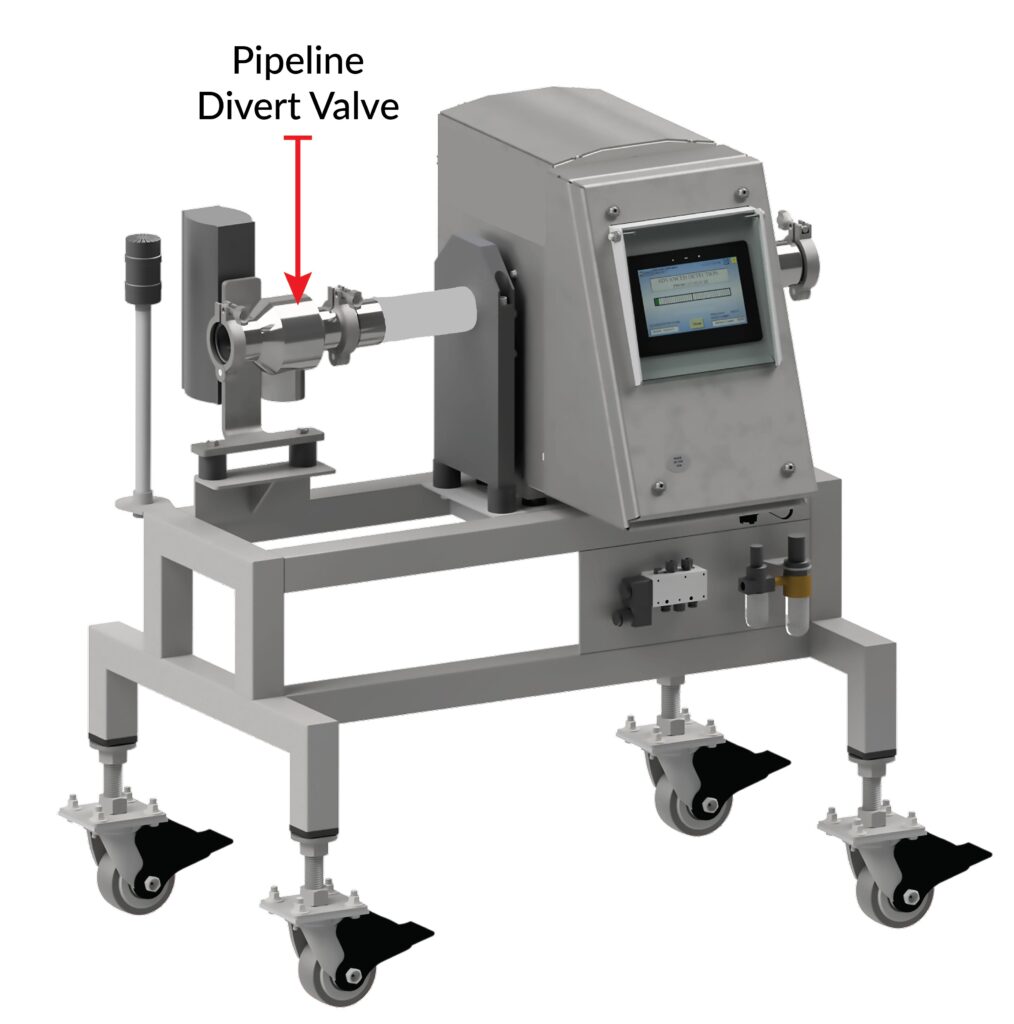
Pipeline Metal Detectors
Pipeline metal detection systems used for pumped products are equipped with automatic 3-way valves that divert contaminated product from the process into an offline container. As with conveyor metal detection the diverted product should be screened, filtered or run through the metal detector again in order to locate the metal contaminant that caused product to be diverted.
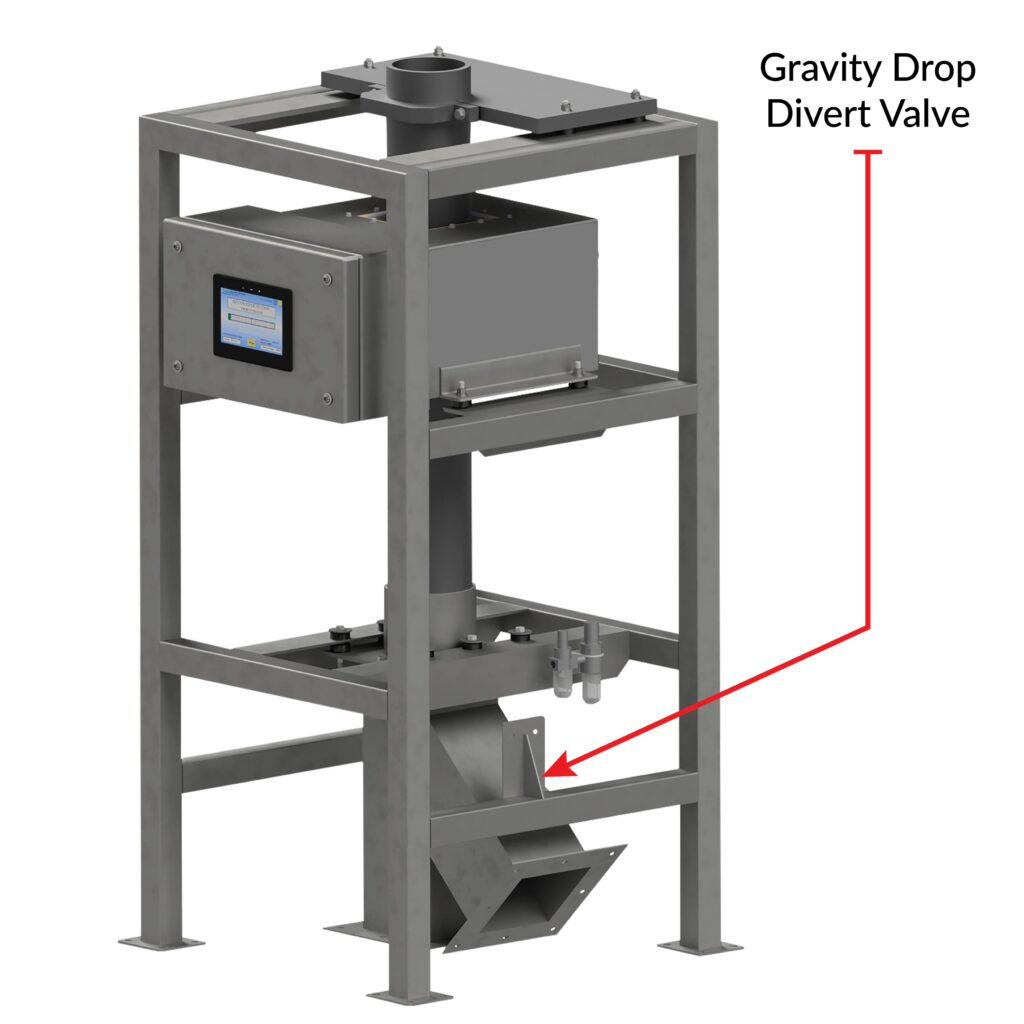
Gravity Drop Metal Detector
Gravity drop metal detection systems for dry, bulk food product can be equipped with a fast acting valve that diverts product from the production process into an offline container. As with pipeline systems the diverted product should be screened or run through the metal detector again to locate the metal contaminant that caused product to be diverted. Sometimes in low volume gravity drop applications where the filling process is manned the gravity drop detector actuates a light and horn upon detect alerting the operator to the presence of metal in the box or bag that is being filled.
Metal Detection Systems for Food Processing & Packaging
Food processing and packaging applications require metal detection systems well suited to your specific process and product. We manufacture a variety of metal detection systems, including conveyor systems, pipeline systems, and gravity drop systems, designed to protect product purity and increase efficiency. Each metal detection system is designed and built to fit your specific food processing or packaging needs. Give us a call at (414)672-0553 or email sales@adsdetection.com to get the best detection results in wet, dry and conductive food.