Advanced Detection Systems manufactures metal detectors designed to provide reliable, easy-to-use and consistent metal detection. Whether you need to ensure product purity or defend processing equipment, getting the best possible metal detector for your application is of utmost importance. Part of ensuring optimum sensitivity is understanding the factors that affect metal detection levels.
Types of Metal
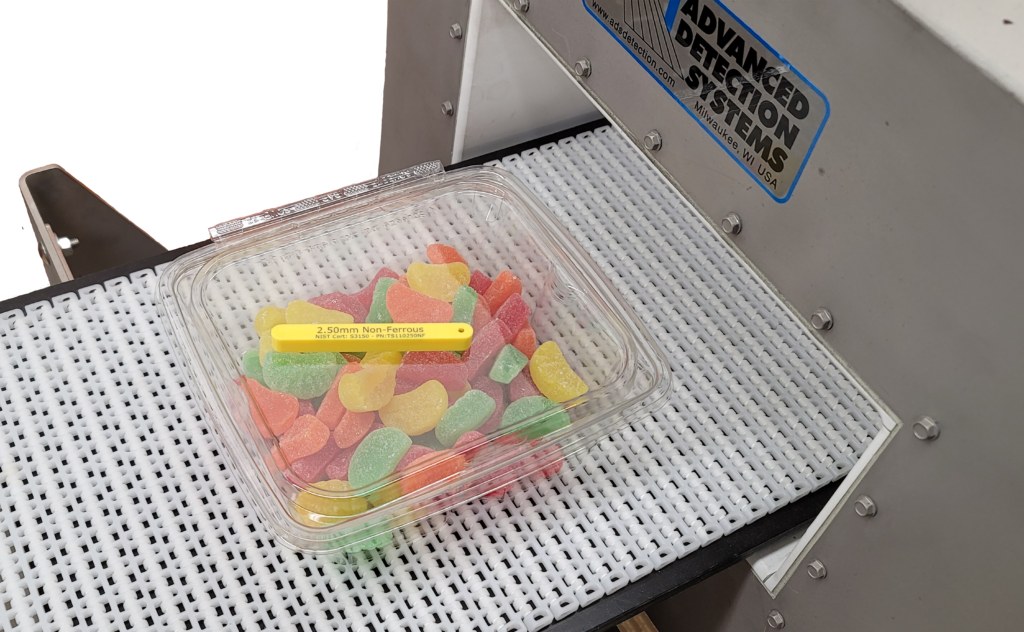
When considering factors that affect the best possible detection levels keep in mind that metal detectors are used to detect particles of Ferrous, Non-Ferrous (aluminum, brass, copper) and Stainless Steel. The accepted method of stating the detectable metal in a particular application is in millimeter spheres. The metal detector’s balanced transmit and receive coils are disturbed by conductivity. Since Ferrous metal is more conductive and magnetic than Non-Ferrous metal or 316 Stainless Steel a metal detector will detect smaller particles of Ferrous than Non-Ferrous or 316 Stainless Steel. Plant managers at food production facilities document the size metal that must be detected by their metal detectors. For example, a metal detection specification of 1.5 mm Ferrous, 1.8 mm Non-Ferrous and 2.0 mm 316 SS reflects the difference in detection level for Ferrous metals, Non-Ferrous metal and Stainless Steel.
Aperture Size
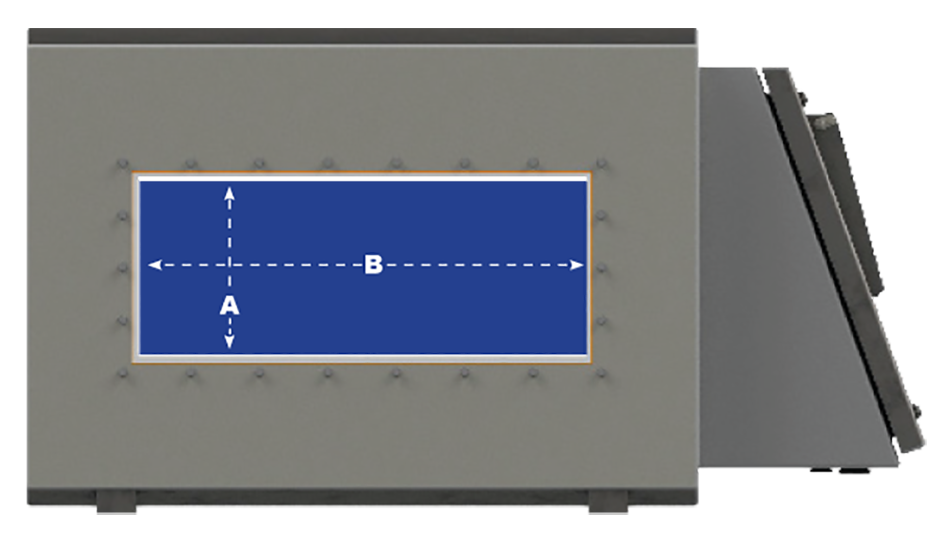
The metal detector’s aperture size is a determining factor in the metal detector performance because the best possible detection level declines as the aperture size increases. The size of the metal detector aperture is determined by the largest package or portion of product passing through the detector at a given time. For instance, a 2 lb package of ground beef measuring 5” wide x 7” long x 2.5” high with the narrow dimension leading will require an aperture 4” high and 8” wide if the ground beef is being conveyed on a 6” wide belt.
Conductivity
The conductive characteristics of the product known as “Product Effect” also affect the best possible detection level because products that are moist, warm or hot and contain salt or fat can be quite conductive. The quantity or orientation of a conductive product also changes the product effect presented to the metal detector.
Metal detectors have an Auto Learn feature that analyzes the conductivity and automatically adjusts the metal detector to accommodate the product effect while detecting metal that is in the product. Given the importance of achieving the best possible detection levels food processors often have their product tested by a metal detector manufacturer to determine the best possible detection levels based on their specific aperture size and product characteristics. Lacking product testing the best possible and reliable detection levels are often established at the in-plant start-up of the metal detection system using the metal detector’s AutoLearn feature.
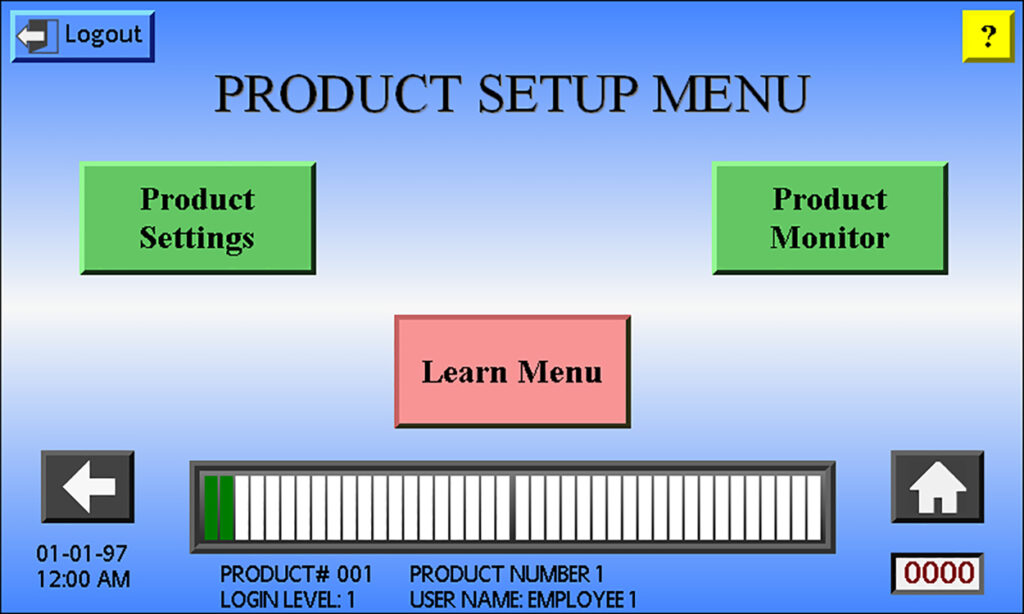
What Metal Detectors Achieve the Best Possible Detection Levels
Given these factors that are known to affect the best possible metal detection levels food processors who produce non-conductive products and are able to use metal detectors with small apertures are expected to achieve better metal detection levels than those producing conductive products and having to use detectors with larger apertures.
Get the Best Metal Detector for your Application
Discuss your application with an Advanced Detection Systems metal detector expert today to determine what is the best configuration for your application. We also offer a free product testing service, providing a Sensitivity Guarantee to indicate the optimal detection levels for your products. Call us today to get started 414-672-0553 or email us at service@adsdetection.com.
David Smith
©Advanced Detection Systems, 2023