When you’re looking at metal detection systems for use in your product line, have you wondered “How small of a piece of metal will this detect?” “How do they determine that?” Good questions!
How is Metal Detector Sensitivity Determined?
Metal detector sensitivity is defined as: The smallest diameter sphere that can be detected, 100% of the time, at the weakest spot in the detector aperture.
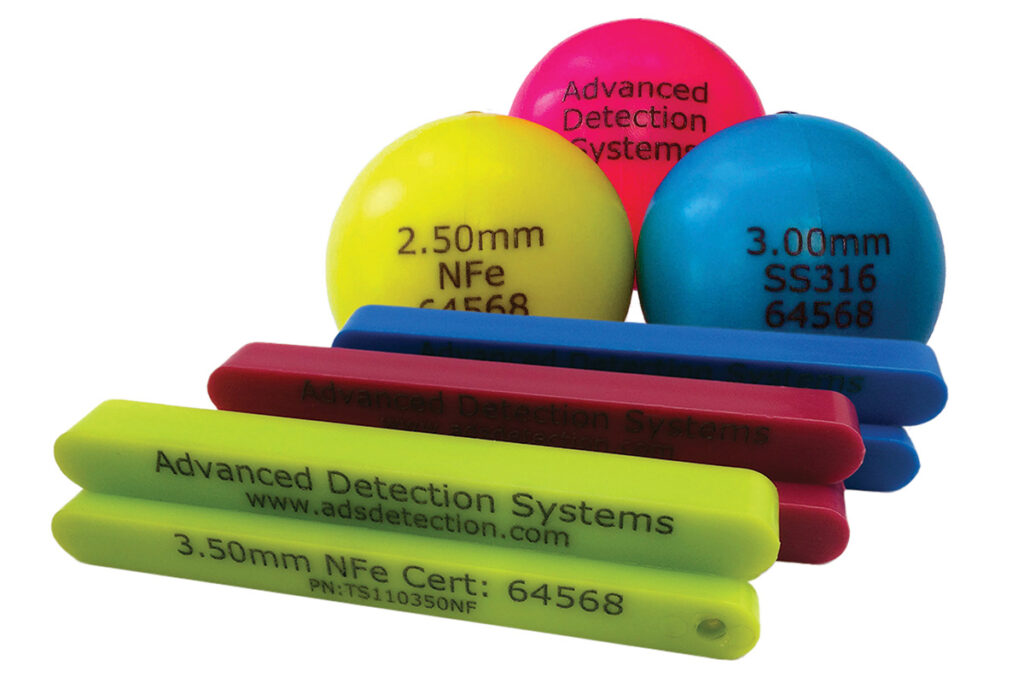
Factors that affect Metal Detection Sensitivity Levels
There are many factors that affect metal detection sensitivity Among them are; the size of the metal detector’s aperture, type of product being inspected, the type of metal, and the shape of the metal. There are others, but let’s look at these.
Metal Detector Aperture size
As might be expected, the larger the size of the aperture, the weaker the sensing field and the less sensitive the detector. This is why it is recommended to select the smallest size aperture for your detector that will fit your application and product dimensions.
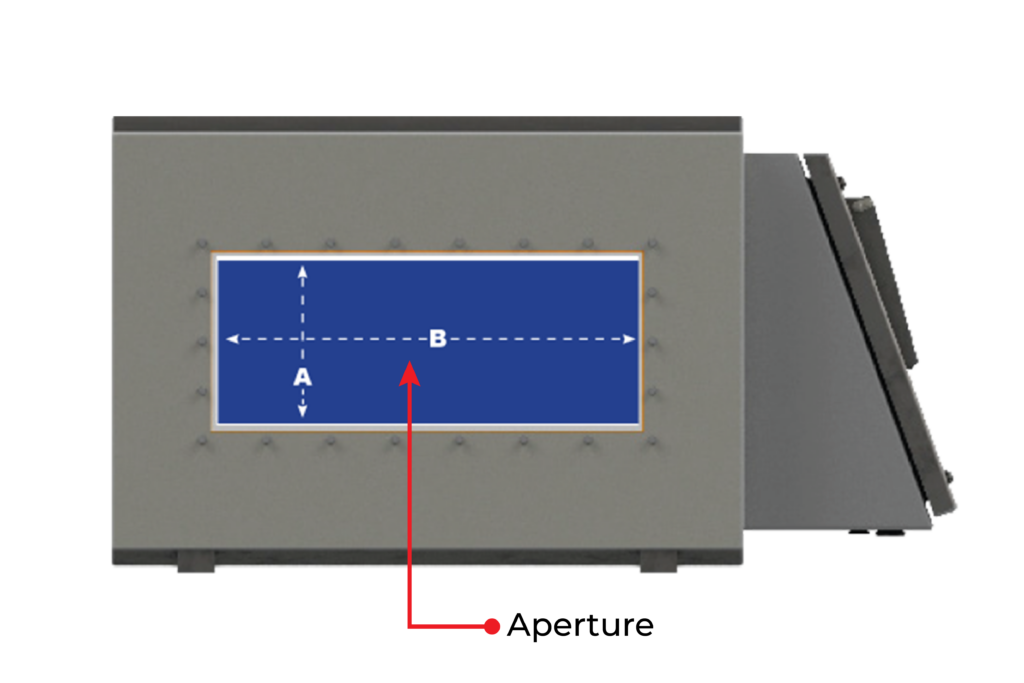
The metal detector’s sensing field is weakest at the geometric center of the opening; the furthest point away from the coils. As you move closer to the perimeter, the field gets stronger and the sensitivity gets slightly better.
Type of Product
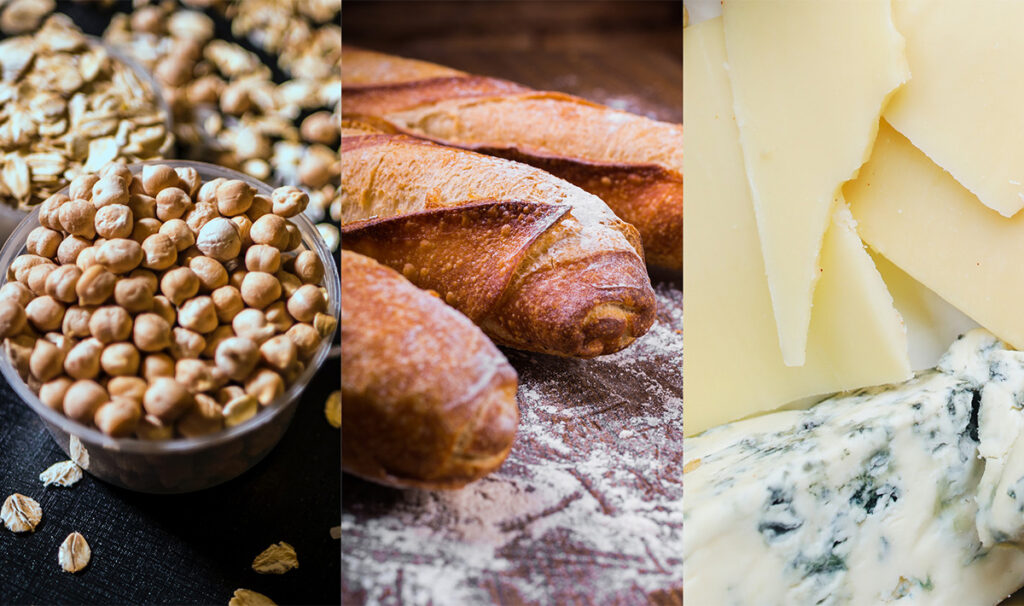
Not only does metal affect the sensing field as it passes through the opening, but also the product will have an effect on the field. The product’s moisture content, salt and mineral content, fat content, temperature, and mass will all have varying degrees of effect on the field. This is called “Product Effect“. That’s why product testing is so important when determining the sensitivity capability of the metal detector.
Type of metal being detected
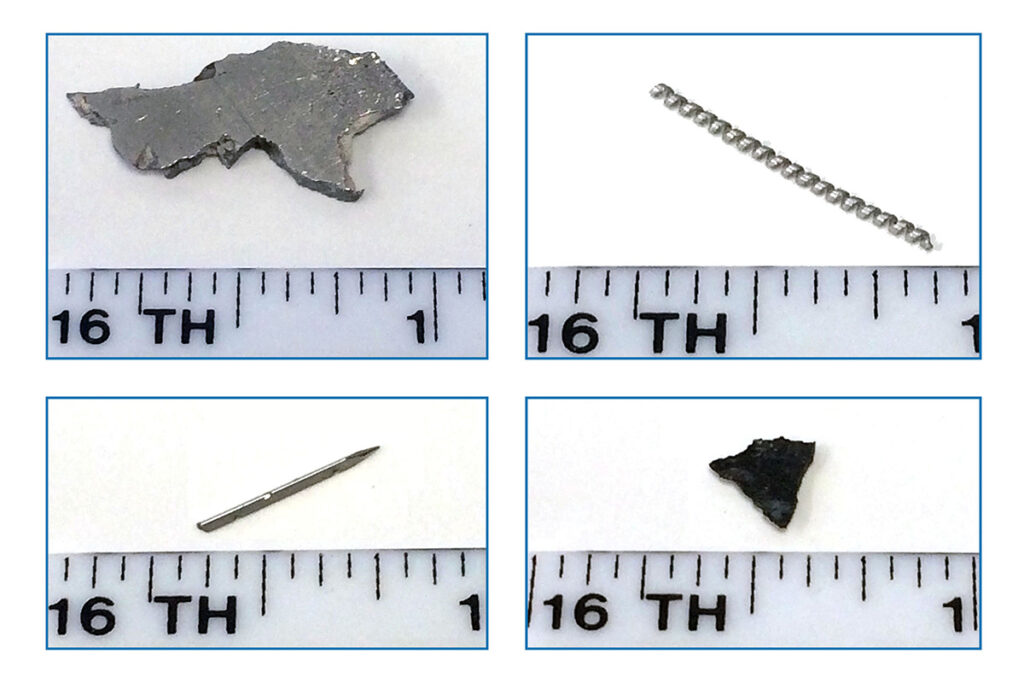
In the metal detection world there are three types of metal; ferrous, nonferrous, and non-magnetic stainless steel. Ferrous metals, such as steel and iron, are the easiest to detect because they have the most effect on the sensing field. Nonferrous metals, such as copper, aluminum, brass, and lead are almost as easy to detect and have a multiplier of approximately 1.1 times ferrous sensitivity. Non-magnetic stainless steels, such as type 302, 304, and 316 are the most difficult to detect and will vary greatly with the type of product but will typically have a multiplier of 1.5 times the ferrous sensitivity.
Example: 1.5mm Ferrous
1.8mm Non-Ferrous
2.2mm Stainless-Steel
Shape and Orientation of Metal
In real world situations, metal contaminants are rarely spherical in shape, except for possibly lead shot. They are generally slivers of metal, turnings, wires or broken machine parts. The orientation of the metal as it passes through the metal detector aperture can determine if the sensing field is affected enough to detect the metal. If the diameter of the sliver or wire is small enough it is possible that quite a long piece could pass through the detector unseen. The better the metal detector’s spherical sensitivity, the better the chance that the slivers and wire will be detected.
The following diagram shows that configuration “A” provides the biggest signal (easiest to detect), in ferrous type wires, while configurations “B” and “C” provide the smallest signal (most difficult to detect). Similarly, in nonferrous and stainless-steel wires the opposite is true (i.e. “A” provides the smallest signal and “B” and “C” provide the biggest signal).
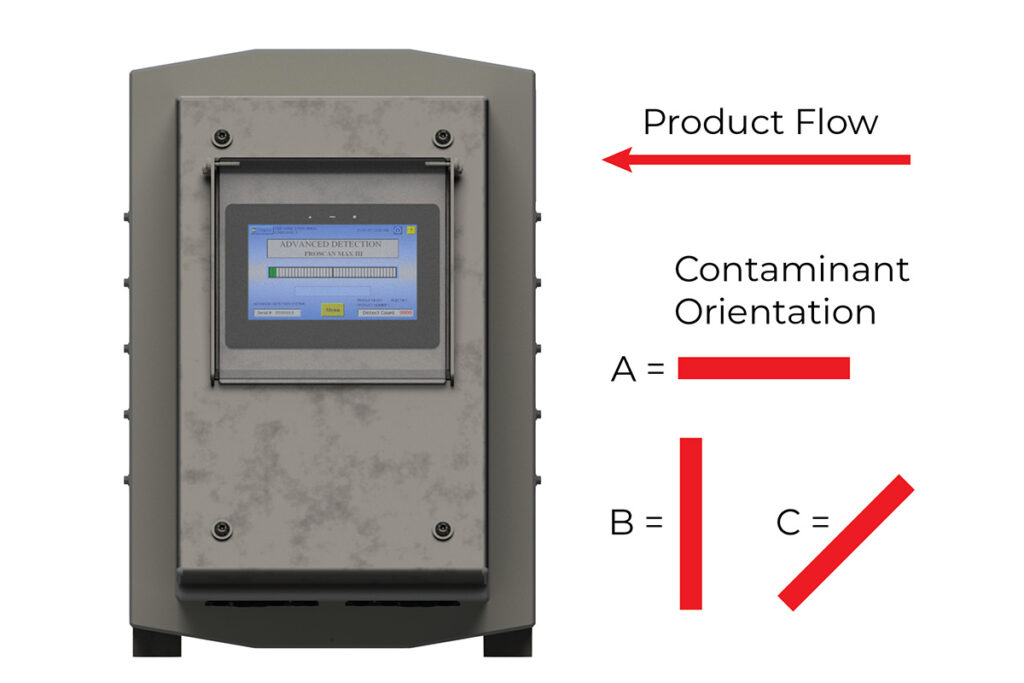
Industrial & Food-Grade Metal Detectors from Advanced Detection Systems
Advanced Detection Systems, in business for 30 years has developed a reputation for manufacturing high quality, reliable metal detection equipment for a variety of food processing and industrial applications. With engineering, manufacturing, sales and customer service staff working side by side in our Milwaukee, WI facility we can provide prompt, expert advice. We’re here to help, call us at (414-672-0553) or e-mail sales@adsdetection.com to discuss your application details and metal detection needs.